One of the most common upgrades or modifications for an FDM printer is the Direct Drive or Bowden Extruder mod. Whether or not one or the other of these mods would best suit your printing needs would be discussed in this article.
Some printers come equipped with a direct drive extrusion system, such as the Prusa i3 MK3 and the Qidi Tech X-Pro, as well as printers that are equipped with the Bowden extruder right out of the box, such as the Creality CR6 SE and the Anycubic i3 Mega S. However, how are they different?
Direct Drive
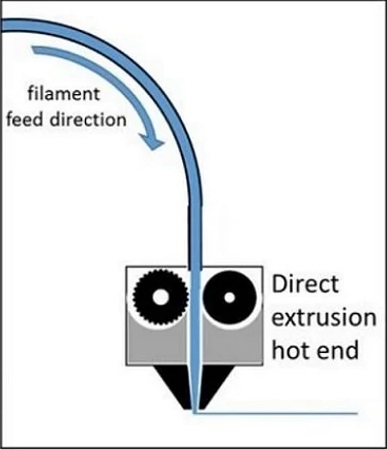

The Direct Drive setup, as indicated by its name, has the extruder “directly” mounted on the hot end assembly and feeds the filament “directly” into the hot end. This popular setup turns the extruder and print end into one assembly. With little space between the extruder and hot end, the distance that the filament must travel is kept at a minimum, which is the main advantage of this setup.
Advantages
- With the distance between the extruder and hot end kept at a minimum, the response time of this setup is short. It creates a more stable material deposition control, which in turn leads to a higher print resolution. Good response time and a stable material deposition control mean better extrusion and retraction.
- Another strength brought about by the closeness of the extruder to the hot end is that less torque is needed from the stepper motor compared to that used in a Bowden Extruder setup. This allows the setup to use smaller and less powerful stepper motors. Although larger, stronger step motors can be beneficial.
- A defining feature of the Direct Drive feature is the wide variety of filaments that it can effectively use. The most notable filaments would be the flexible and abrasive ones, such as wood filaments.
Disadvantages
- This setup has two disadvantages, one of which some may consider as a deal-breaker. The first disadvantage is the vibrations and wobbles due to the heavy print head assembly. With the weight of the print head assembly and the speed constraints, constantly moving causes banding, overshoot, and frame wobble, not to mention the weight added to the z-axis gantry. Some users opt to upgrade the z-axis with a linear rail instead of the stock roller, while some print at lower speeds to minimize the wobble.
- The disadvantage that some may see as a deal-breaker is the maintenance. A clog in a direct drive setup requires the whole assembly to be taken apart to unclog the system.
Bowden Extruder
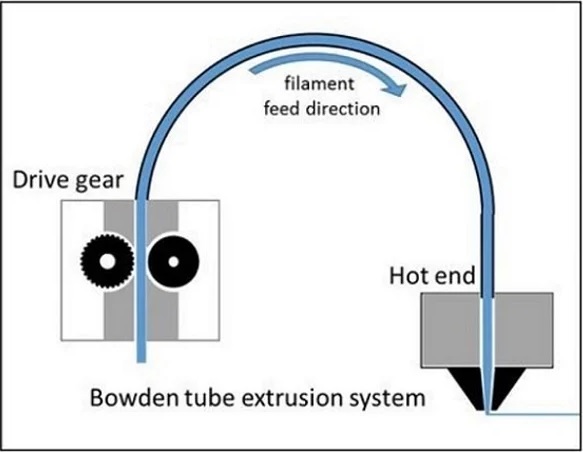

The Bowden Extruder setup involves the extruder NOT being attached to the hot end or print head. Instead, the extruder is commonly attached to the printer’s frame and feeds the filament to the hot end via the bowden tube, usually referred to as the PTFE (Polytetrafluoroethylene) tube.
Advantages
- The main strength for this setup is the lightened load on the hot end assembly, allowing the print head to operate faster. With less weight, the movements and jerks create less wobble, little to no overshooting, and less banding. This makes the overall print quality more accurate.
- With the extruder and hot end assembly being two separate assemblies, maintenance on each assembly does not require the takedown of both assemblies, like that of the direct drive setup. If the hot end has a clog, there is no need to separate or detach the extruder.
Disadvantages
- Depending on what the user usually wants to print, this disadvantage can either be minor or significant: a limited variety of usable filaments. With a Bowden extruder setup, abrasive and flexible filaments are a no-go. The abrasive filaments would wear away and damage the insides of the Bowden tube. While it’s possible to print flexible filaments, it is likely for the flexible filament to bind in the Bowden tubing, leading to clogs and possibly damaging the extruder.
- With the good amount of distance between the extruder and the hot end, the Bowden extruder setup requires a greater retraction distance to avoid stringing and overflow/oozing during print.
- Due to the distance and friction brought about by the Bowden tube, the setups require a stronger step motor.
Which to Choose?
It all falls down to what kind of prints you will be doing and how much time and effort you would put into maintenance. Direct Drive extrusion outperforms the Bowden extrusion, allows for a wider range of materials, and has a better material deposition control. The Bowden extrusion, however, offers easier maintenance and faster prints.
A condition that supersedes the former, though, is the type of printer. Delta printers cannot support direct drive. Cartesian and CoreXY printers can, but it also depends on the stability of their frames.
References
Creality. (2020 July 27). Direct drive vs Bowden extruder. Retrieved from: https://www.creality.com/blog-detail/3d-printer-direct-drive-vs-bowden-extruder
Hullette, T. (2021 March). Direct drive vs Bowden extruder setup: the differences. Retrieved from: https://all3dp.com/2/direct-vs-bowden-extruder-technology-shootout/
n.a. (2017 November 30). Advantages and disadvantages of direct and Bowden extrusion. Retrieved from: https://www.fargo3dprinting.com/advantages-disadvantages-direct-bowden-extrusion/
Airwolf