The Role of Actuators in CNC-Driven Robotics – Actuators are fundamental parts of many enterprises, assuming an urgent part in changing input energy into mechanical movement. They are liable for controlling and moving different frameworks and gadgets, empowering exact and effective activity. As the interest in computerization and cutting-edge innovations keeps on developing, the significance of actuators in applications like advanced mechanics, auto, aviation, modern mechanization, and clinical gadgets couldn’t possibly be more significant.
An actuator is a machine, or rather a piece of a machine used to change remotely accessible energy into movement given the control signals. Similar to how hands and legs empower people to move around and perform activities, actuators let machines perform different mechanical developments. In this article, Circuitrocks will make sense of what an actuator is, the way actuators work and the job of actuators in CNC-driven mechanical technology.
Two fundamental steps are required for robots to interact with the real world: The first thing they need to do is get a sense of their surroundings, and then they need to take action based on that data by navigating to avoid obstacles or manipulating objects. The actuator, a component that transforms electronic commands into actual movements, is relied upon by developers of robotics when it comes to navigating the environment and manipulating objects.
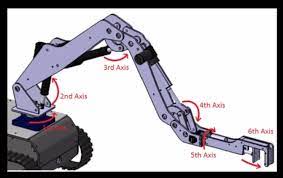
Types of Actuators
Five general Types of actuators automated engineers integrate into their activities:
- Motor DC: an engine with a result shaft driven by DC voltage at different levels, and utilized essentially with drivetrains for portability (e.g., a crawler). The output shaft of a DC motor is typically connected to a pinion, spur, or other kind of gear and wired to an electronic speed controller that controls the speed and rotational direction of the motor. DC engines, as different actuators, are accessible in various sizes and force taking care of attributes.
- Servo: a part with a DC engine, yield shaft, and control hardware all bundled into one unit. Servos for the most part give rotational development, aside from persistent pivot servo variations that can turn 360 degrees. There are leisure activity grade and mechanical grade servos which we’ll examine later in this blog.
- Stepper: a cross-breed between a DC engine and a servo. Steppers are in many cases utilized in 3D printers and CNC machines for high precision and repeatability, frequently where lower force yield is adequate.
- Linear Actuator: like a servo yet gives straight movement, frequently through direct systems, for example, worm drives.
- Solenoids: a particular sort of straight actuator that can expect double positions (i.e., on/off, open/shut, and so on.). Solenoids are normally utilized for applications like valves, hooks, and locks, or for pressing buttons, and are typically constrained by an outer microcontroller.
The Role of Actuators in CNC-Driven Robotics
There are a lot of factors to consider when selecting actuators because robots can be constructed for a variety of purposes, functions, and operating environments.
The sort of actuator expected for a provided application will rely upon the robot’s motivation and planned usefulness. For instance, a DC engine will probably be utilized related to a drivetrain to consider portability, while a servo might be utilized to explain that tracked down in a mechanical arm.
When the kind of actuator has been chosen, designers ought to check out the actual necessities and requirements. The actuator’s physical size and weight are the first things to check to see if it will fit where it is needed and if the actuator and mechanism on which it is mounted weigh enough. For instance, putting a weighty actuator on a little, frail mechanical arm might cause the arm bomb under its own weight.
More Applications
One more actual viewpoint to take a gander at is the computerized interfaces accessible on both the actuator and the microcontroller liable for controlling it. For instance, servos by and large have three wires including ground, power, and a control signal. Depending on the actuator’s power requirements, you might be able to power it directly from the microcontroller, but in other cases, you might need to get power from somewhere else (for example, microcontrollers typically only have a range of about 5 VDC).
Contingent upon their planned use, designers ought to guarantee that a given actuator is sufficiently able to take care of business. For instance, a DC engine should be chosen with the end goal that it gives sufficient capacity to the drivetrain to move the robot and the robot’s heap in the working climate.
Last but not least, the protocol for communication must be taken into account. Numerous actuators support correspondences utilizing pulse width modulation (PWM) while some might uphold sequential interchanges.
Conclusion
Actuators are fundamental parts of many enterprises and applications, giving exact control and development because of different data sources and conditions. However, developments in the area get little inclusion in the media contrasted with state-of-the-art advances like Man-made consciousness (computer-based intelligence), Blockchain, Web of Things (IoT), 3D printing, and so on.
Engineers and designers need to know about the principles, types, and performance metrics of actuators. They also need to know what to look for in an actuator when choosing one to get the best performance, efficiency, and reliability.
As innovation keeps on propelling, the improvement of imaginative actuator arrangements will stay a vital area of concentration, driving upgrades in different fields, including auto, aviation, and modern mechanization.