Tips To Choose Prototyping Components – Prototyping material selection is an important part of product development. Developing a prototype is crucial to guarantee that a product is functional, efficient, and effective. Before beginning mass production, a prototype allows you to test and validate your design and detect any possible issues. However, selecting the right prototyping material might be a big challenge.
In this article, Circuitrocks will cover the different types of prototyping materials, the factors to consider when choosing a material, and tips to choose prototyping components. This way, you could better choose the suitable material for your project.
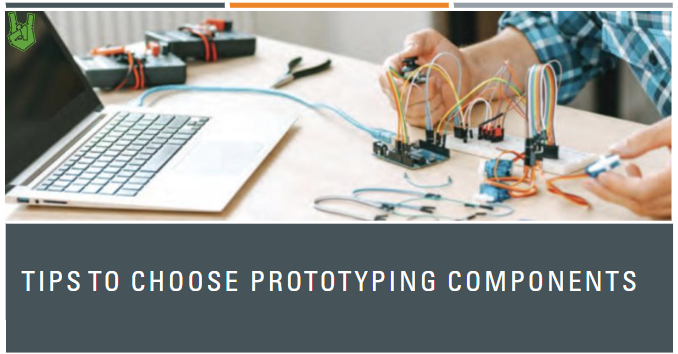
Factors to Consider When Choosing Prototyping Materials
When selecting prototyping materials, several factors should be taken into consideration, including the following:
- Cost: Because the costs of the parts might range quite a bit, it is essential to consider a budget for the undertaking.
- Durability: Certain products require great strength or durability. Selecting materials that can endure the stresses imposed on them is essential.
- Functionality: Certain materials may be more suited for certain functions, such as insulating, absorbing shock, or conducting electricity, respectively.
- Manufacturing Method: The manufacturing process that will be utilized for the final product may also impact the selection of materials used for the prototype.
- UV Resistance: Materials exposed to sunlight or UV radiation may require resistance to prevent degradation.
- Sound and Vibration Characteristics: Moreover, Materials used in acoustic or vibration-related applications should have suitable acoustic and vibration-damping properties.
- Transparency or Opacity: The level of transparency or opacity can be crucial for prototypes involving displays, lenses, or visual elements.
- Ease of Prototyping: Some materials are better suited for specific prototyping methods, such as injection molding, 3D printing, etc.
- Ease of Machining: Further, Consider how easily the material can be shaped, cut, or molded to create your prototype’s desired form.
- Availability and Recyclability: Ensure that the chosen material is readily available and accessible for your prototyping needs. Also, Sustainability concerns may lead you to select materials that are recyclable or have a minimal environmental footprint.
Tips to Choose the Right Prototyping Components
- Functional Requirements: What properties must the material possess to meet the functional needs of your prototype?
- Define Project Requirements: Clearly outline the specific requirements of your project. Consider factors like strength, durability, aesthetics, cost, and any unique properties needed.
- Understand Material Properties: Research and understand the properties of available materials. Consider strength, flexibility, thermal conductivity, and other relevant characteristics.
- Budget Considerations: Can you afford the material within your budget for prototyping? Evaluate your budget constraints. Some materials may be more cost-effective for your project than others.
- Prototyping Method: Determine your prototyping method (e.g., injection moulding, 3D printing, CNC machining). Some materials are better suited to certain techniques.
- Functional Needs: Assess whether the material can fulfil the functional requirements of your prototype. Will it withstand the intended use and environment?
- Aesthetic Requirements: Consider how the material’s appearance aligns with the desired look and feel of your prototype. Aesthetics can be crucial for user testing and presentations.
- Environmental Impact: If sustainability is a concern, opt for materials with eco-friendly properties or recyclability.
- Regulatory Compliance: In industries with strict regulations (e.g., medical or aerospace), ensure the chosen material complies with relevant standards.
- Manufacturability and Lead Times: Check if the material is readily available and if lead times for procurement align with your project timeline.
- Material Testing: If necessary, conduct material testing to confirm that it meets your project’s requirements.
- Consult Experts: Seek advice from experts or colleagues experienced in your field for material recommendations.
- Iterate: if necessary be open to adjusting your material choice if initial prototyping reveals unforeseen issues or limitations.
- Documentation: Maintain thorough records for material selection, including properties, sources, and test results for future reference.
Most Common Prototype Materials to Make a Prototype
Common prototype materials encompass a diverse range of options, each suitable for specific applications and industries. Here are some common prototype materials:
Plastics
- Plastics are a versatile category of prototype materials widely used due to their adaptability and cost-effectiveness.
- Various types of plastics, such as ABS, PLA, polycarbonate, and acrylic, offer different properties to suit specific applications.
- ABS is durable and often employed in functional prototypes.
- PLA, biodegradable and easy to 3D print, is ideal for concept models.
- Polycarbonate’s strength makes it suitable for robust prototypes.
- Acrylic, transparent and visually appealing, is used for visual prototypes and displays.
Metals
- Metals like aluminum, steel, and titanium are chosen for their strength and durability.
- These are indispensable in prototype development due to their strength and durability.
- Rubber and Silicone
- These materials are ideal for prototypes involving seals, gaskets, or flexible components, common in automotive and medical industries.
- Also, Their unique properties include elasticity, flexibility, and resistance to heat and chemicals.
Ceramics
- Ceramics are chosen for prototypes requiring high-temperature resistance and electrical insulation, such as electronic components.
- Moreover, They’re employed in industries like electronics, aerospace, and medical devices to prototype components that require these characteristics.
- Ceramic prototypes ensure functionality and reliability under extreme conditions, such as in the production of heat-resistant electronic parts or medical implants, where electrical isolation and biocompatibility are crucial.
Bio plastics
- These environmentally friendly plastics are made from renewable sources like cornstarch, sugarcane, or potato starch, and are suitable for sustainable product prototypes.
- They are used in prototype development with an environmental focus.
Conclusion
By following these steps and carefully considering the specific needs of your project, you can make an informed decision when choosing the right material for your prototype. Also, setting the stage for a successful product development process. Choosing the right prototyping material is a crucial step in the product development process. Moreover, It impacts not only the functionality and appearance of your prototype but also your project’s overall success. By carefully evaluating your project’s requirements and considering the properties of various materials, you can make informed decisions that will lead to a successful prototype and, ultimately, a successful product.